Mechanical testing refers to the physical testing of materials and products such as metals, plastics, rubber, textiles, timber, lifting gear, pipes, valves and automotive products. Mechanical testing is performed to determine various mechanical properties of materials such as strength, hardness, ductility, toughness, brittleness, etc. There are several types of test to determine various mechanical and physical properties of material. The precision results of these tests is utilised to determine suitability of materials for the field application.
Macroscopic Examination
Macro test or macro examination is performed on the cross section, longitudinal section or āZā direction ( through thickness) as an independent test to evaluate subsurface conditions or as an subsequent step of another test to reveal the effects on the subsurface.
Generally macro test or examination is performed at less than 10x magnification. Several semi-finished and samples of finished products are subjected to macro test to reveal internal discontinuities such as impurities, inclusions in rolled products or grain flow in forgings after exposure to appropriate preparation and exposure to chemicals or heat.
The most common test is weld cross section examination to reveal internal discontinuities, weld profile, weld passes and sequence, extent of penetration and the quality of weld.
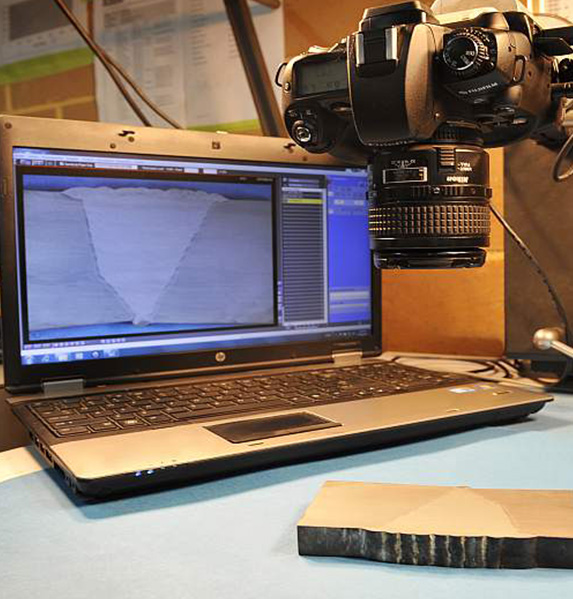
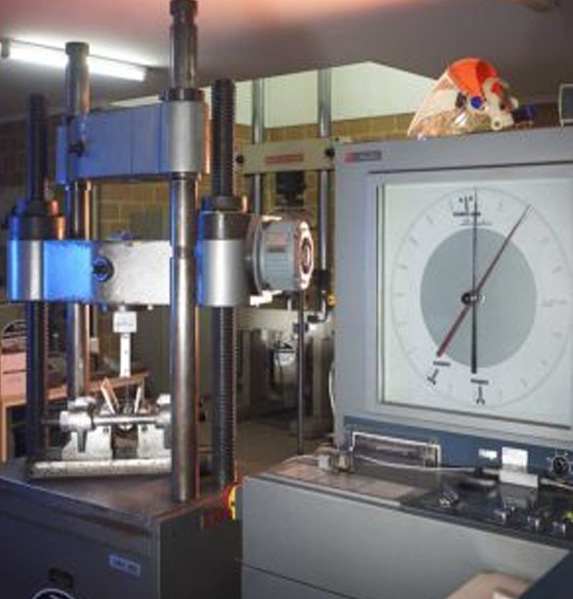
Tensile / Compression Testing
Tensile test is the most elementary type of mechanical test performed on materials. Tensile tests are simple, economical and traceable to the national standards. A tensile test also known as tension test is performed by holding the test items or test specimens in a suitable equipment. An axial pulling force is applied on the test item or test specimen and its behaviour under force is recorded on a conventional graph or chart or computerised data acquisition method.
Generally this test is performed at ambient temperature. Where a material is subjected to elevated temperature such as boilers and pressure vessel applications, a high temperature tensile test is performed. This test provides information such as Proof load, 0.2% proof stress, Yield strength, Ultimate tensile strength or breaking force, Elongation, Reduction of area, modulus of elasticity, etc
Bend Testing
A bend test is a type of mechanical test performed on metals in which a sample is bent around a given or calculated bend radius. Bend tests are used to evaluate the ductility and soundness of a welded joint. In most cases bends are taken transverse to the weld axis and are bent in a plunger type test machine (3 ā Point Bend).
Face bends are performed with the face of the weld in tension, and root bends are performed with the root of the weld in tension. Often when testing materials with thickness >10mm side bend specimens are prepared and bent with the welded cross section in tension. This type of testing is particularly good at finding fusion defects, which open up in the surface during the bending operation.
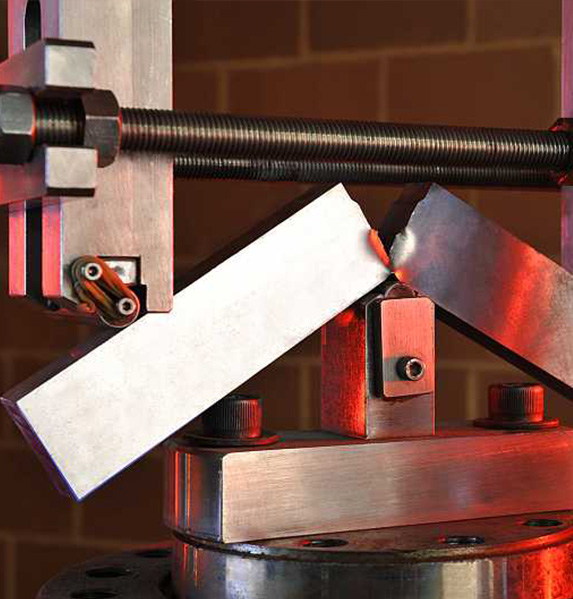
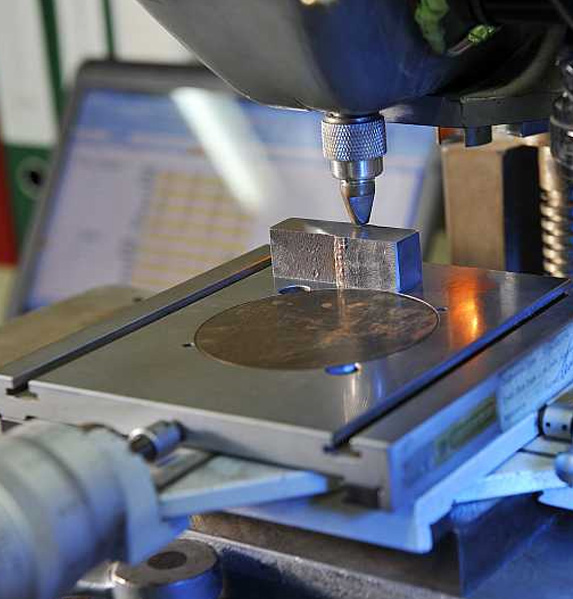
Hardness Testing
Hardness is a mechanical property of material which refers to resistance to plastic deformation by indentation under applied force.
Hardness is very common terminology used by almost every engineering person to describe materials behaviour in terms of hard, soft, machinability, strength, etc.
Hardness values are used as a reference to determine materials machinability, ductility, elasticity, malleability, brittleness, toughness, strength in various modes and wear resistance.
The most common laboratory based hardness tests are Rockwell hardness, Vickers hardness, Brinell hardness.
Other Mechanical Testing Services
- Shear Test
- Bend Test
- G48 Corrosion Test
- Impact Test
- Onsite Machine Workshop
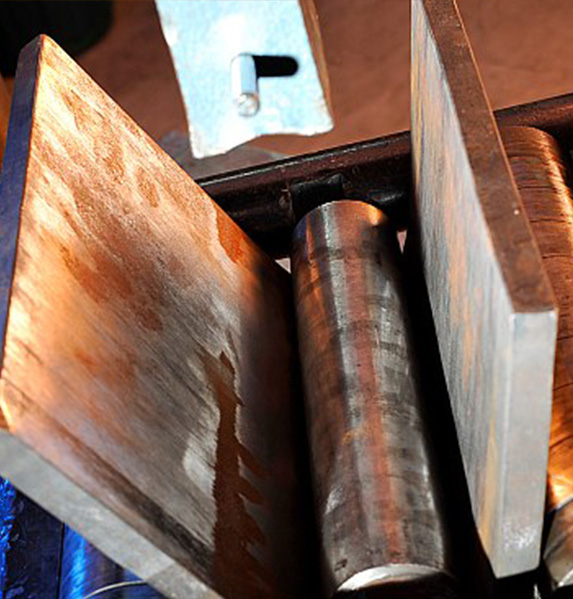